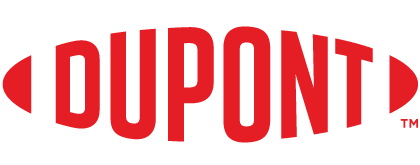
Job Information
DuPont KSW/CRL Area Specialist in Circleville, Ohio
At DuPont, we are working on things that matter; whether it’s providing clean water to more than a billion people on the planet, producing materials that are essential in everyday technology devices from smartphones to electric vehicles, or protecting workers around the world.
If you would like to be a part of a premier multi-industrial company that is delivering sustainable solutions that bring real purpose and value, of a company with collaborative spirit because it believes that we work best when we work together as a team and values the diversity of thought, then DuPont is the company for you!
WHY JOIN US?
Our purpose is to empower the world with essential innovations to thrive. We work on things that matter!
Have the Opportunity to chart your own course, challenge yourself, and acquire new capabilities to build a rewarding and fulfilling career. We reward employees with competitive pay and incentives to recognize skills, competencies, and contributions to business results.
Get to Experience a collaborative environment where teamwork is celebrated with flexibility that enhances balance and an inclusive atmosphere that is welcoming to all!
Get to know our Purpose and make it yours by bringing innovations to market that improve the world, share a commitment to sustainability that makes our planet better and give back to communities in which we work and live.
The Circleville Plant is hiring a Kapton® KSW/CRL Area Specialist This role will have responsibility to schedule maintenance or Asset Care activities for the area assets associated with KSW and CRL by balancing the production/CRL lab requirements with Maintenance and Engineering activities.
Your Key Responsibilities:
Ensures equipment is available to meet production/lab demands in ways that optimize total business cost (production downtime, maintenance cost, MRO inventory cost, etc.). Understands the needs of production schedules and the windows for maintenance and capital activities to occur.
Maximizes the production job steps including decommissioning, lockout, line breaks, and re-commissioning plus the maintenance and capital work to ensure successful integration to minimize cost and production downtime.
Coordinate/negotiate with all stakeholders to attain the best business solutions.
Uses acute understanding of the area procedures and the process to provide analysis, give instruction, plan, compile information, and work with supply chain or upstream/downstream customers to coordinate efforts.
Draws upon significant production area experiences with the equipment and the process to make business-based decisions.
Has responsibility for assessing the quality, robustness, and capability of the process and making decisions, with others, to halt or modify production as needed should the process not meet quality and/or safety standards.
Understand the Production strategy (goals), how it pertains to operating the production process, and how equipment effectiveness and availability impacts the Production strategy.
Understands the KSW/CRL equipment/building needs.
Lead integration of the Work Management Process (WMP) into the production, maintenance, and engineering cultures at KSW/CRL.
Develop schedules for downtime activities and turn-arounds (TARs).
Support the integration of the Reliability Management Process (RMP) into the production culture.
Production representative in the MRO Inventory managing process(es) that is led by the MRO Planner.
Ensure timely completion critical preventive maintenance.
Lead and participate in area audits and investigations (safety and quality).
Lead several PSM elements – Element Lead for Incident Reporting and Investigation Reporting/Contractor Safety/Auditing.
Operating procedure accuracy/creation.
Responsible for Training Plans for the area.
Initiate Management of Change (MOC).
Main contact for contractors and vendors.
Qualifications:
HS Diploma Required 2-year technical degree or equivalent experience preferred.
Five years’ experience in a dynamic manufacturing environment.
Proficiency with SAP transactions, MS Word and Excel.
Strong organizational, communication, and interpersonal skills.
Ability to interact, coach, and provide guidance to colleagues at all levels, which includes the ability to lead teams to achieve desired results.
Self-managed / self-motivated and able to work without close supervision.
Demonstrated leadership ability, primarily through influence, to achieve results.
Understand hazards, failure modes, and the complexity of various maintenance restoration techniques to effectively integrate into the scheduling process.
Working knowledge of the Kapton® Manufacturing area.
Demonstrated troubleshooting and problem-solving skills.
Knowledge of and experience with Site Safety policies, procedures, and training.
Understand all 14 spokes of the Process Safety Management (PSM) wheel and understand their role for each spoke (focus on MOC, PSSR, contractor safety, Mechanical Integrity, etc. in this role).
Mechanical aptitude – ability to work with operations to understand and convey equipment issues or needs to the maintenance and technical organizations.
Preferred Qualifications:
Previous Casting area manufacturing experience, which includes knowledge of and experience with various processes, equipment, products, and dynamic work environment needed to meet business needs.
Previous maintenance or maintenance coordinator experience.
Knowledge of required lock-out boundaries to conduct effective asset care activities.
Experience with root cause failure analysis, troubleshooting & why tree methodology. Incident Investigation Training (can be acquired while in role).
Six Sigma Green Belt Certification (can be acquired while in role).
Lean Manufacturing certification or training (can be acquired while in role).
PSM Training (can be acquired while in role).
Join our Talent Community (http://careers.dupont.com/us/en/jointalentcommunity) to stay connected with us!
DuPont is an equal opportunity employer. Qualified applicants will be considered without regard to race, color, religion, creed, sex, sexual orientation, gender identity, marital status, national origin, age, veteran status, disability or any other protected class. If you need a reasonable accommodation to search or apply for a position, please visit our Accessibility Page for Contact Information (http://www.dupont.com/global-links/accessibility.html) .